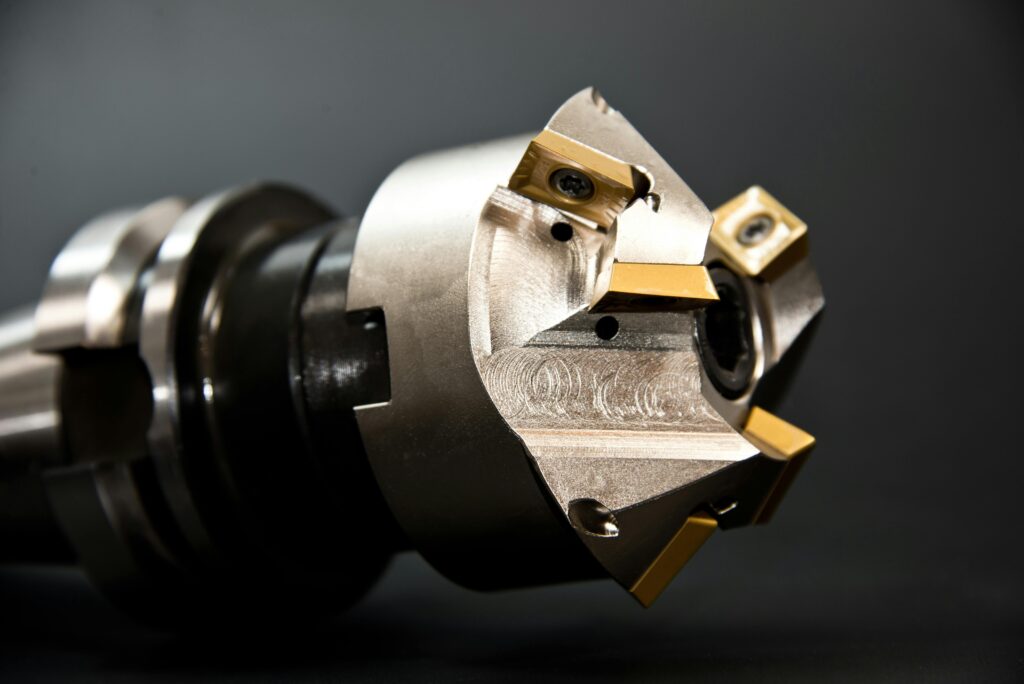
CNC Machining
Precision Machining for Die-Cast Components
Vormetal offers in-house CNC machining services as an essential part of our end-to-end die casting solutions. Our CNC capabilities allow us to deliver precision-machined components that meet tight tolerances, critical surface requirements, and complex design specifications across various industries.
By combining CNC machining with pressure die casting under one roof, we streamline production, reduce lead times, and ensure consistent quality throughout the entire process chain—from raw casting to finished part.
Our CNC machining centers are specifically configured to handle the demanding post-processing requirements of complex die-cast components, particularly those made from aluminum and zinc alloys. With advanced multi-axis capabilities, we are able to machine intricate geometries and fine details with consistent precision across small and large batch volumes.
Our in-house machining processes include multi-axis milling, high-speed turning, drilling, tapping, and surface refinement—ensuring that each component meets all dimensional, functional, and cosmetic specifications as defined by the customer or application.
Key capabilities include:
- Multi-spindle CNC turning
- 3- and 5-axis CNC milling
- Precision boring, threading, and surface detailing
- Tight tolerance machining down to ±0.01 mm
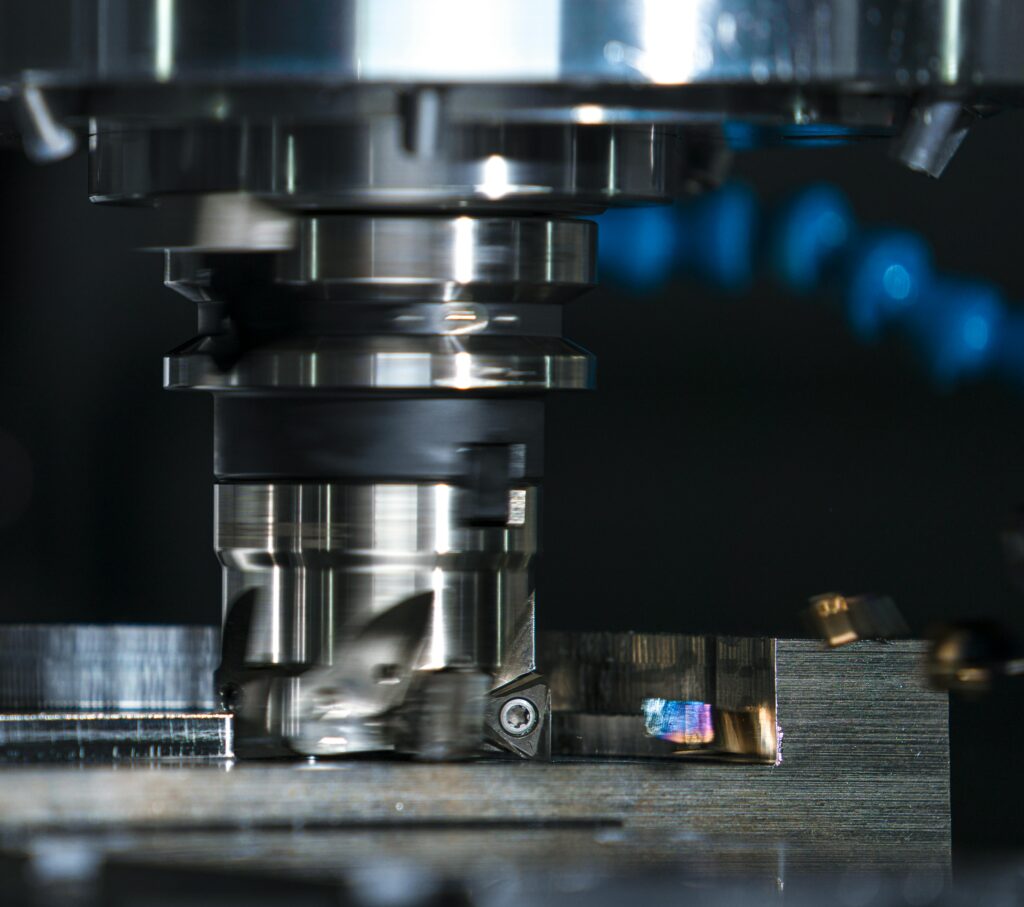
Applications Across Key Industries
Machined die cast parts from Vormetal are used in a variety of demanding applications, including:
- Automotive – brackets, housings, transmission components
- Aerospace – lightweight, high-precision structures
- Industrial – gearboxes, valve bodies, sensor enclosures
- Electronics – heat sinks, EMC-shielded enclosures
Advantages of Our Integrated Approach
Combining CNC machining with in-house die casting allows Vormetal to offer several key benefits over traditional subcontracted approaches:
- Seamless workflow from casting to final machining
- Reduced transportation costs and coordination overhead
- Improved traceability and quality control
- Faster turnaround for engineering changes or customizations
Quality You Can Measure
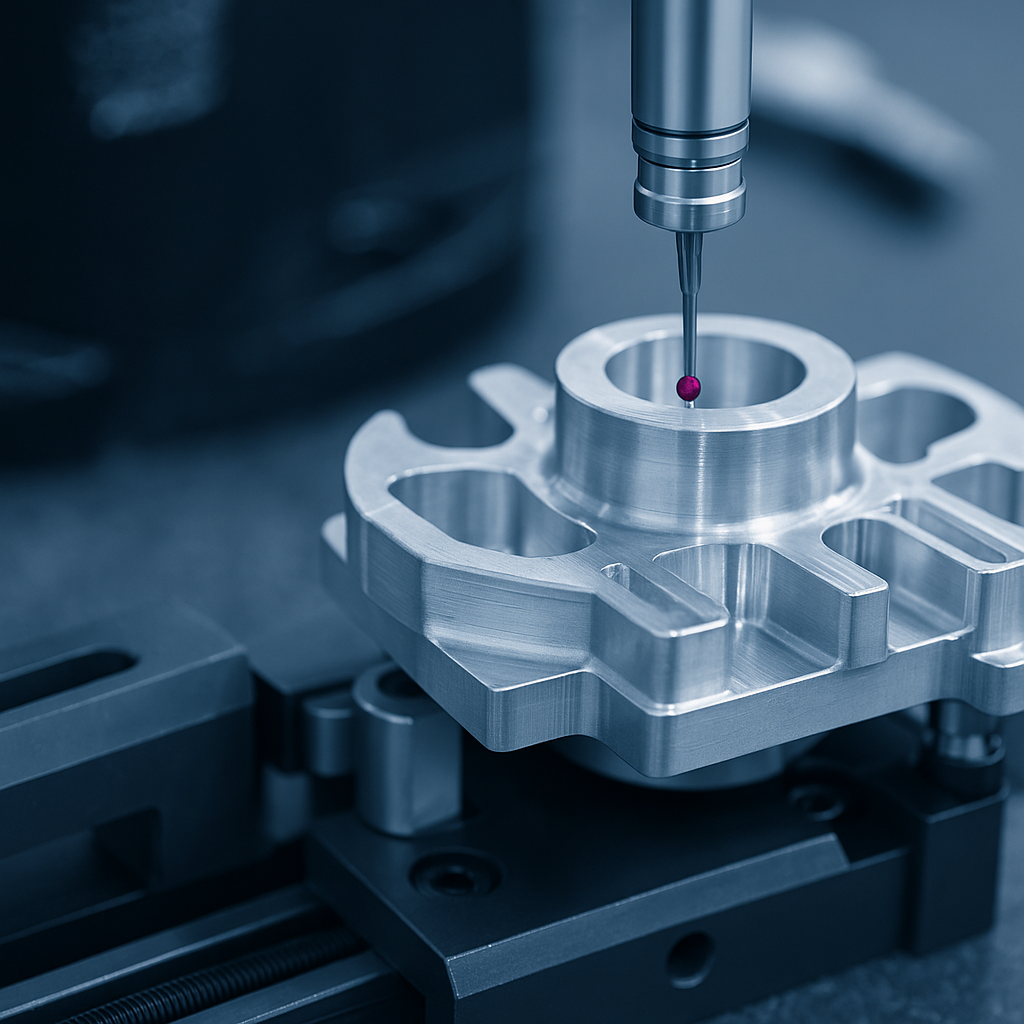
All machined components produced by Vormetal are subject to stringent quality control procedures to ensure they meet the highest standards of accuracy and reliability. Our quality assurance process is supported by a dedicated metrology department equipped with state-of-the-art inspection technologies, capable of verifying even the most demanding dimensional and geometric specifications.
We utilize coordinate measuring machines (CMMs) for 3D dimensional verification, optical inspection systems for non-contact surface and feature analysis, and surface roughness testers to validate finish and texture according to customer-defined tolerances. These tools allow us to accurately inspect and document part conformity throughout the production lifecycle.
Each part is measured and validated against the original CAD data, geometric dimensioning and tolerancing (GD&T) requirements, and any applicable industry-specific standards, ensuring that every finished component is delivered within spec and ready for integration.
Request a Quote or Learn More
If you require machined aluminum or zinc die-cast components with precision-critical features, Vormetal is ready to support your production goals. Our engineering team is available to provide design input, lead time estimates, and tailored quotes for your specific project.