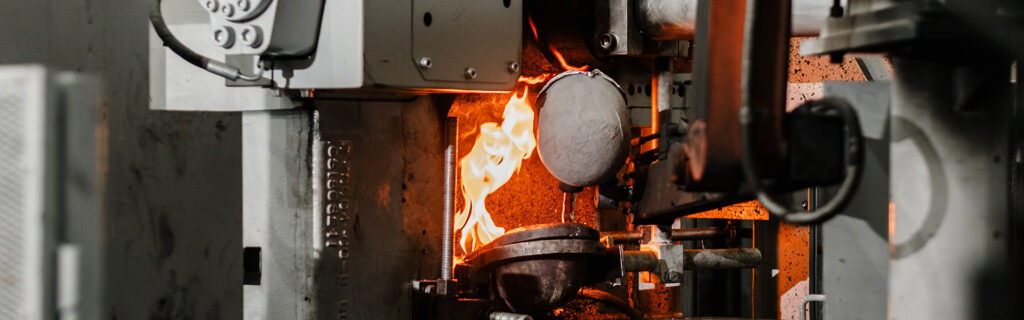
Understanding the Die Casting Process – Step by Step
Die-casting can turn a pile of metal bars into precise, complex components in minutes.
If you are not a foundry specialist, the details may sound mysterious. Below, the workflow is explained step-by-step—using everyday words, minimal symbols, and only the numbers you need.
Melt the Metal and Check the Alloy
- Start with clean ingredients.
New ingot supplies the base metal.
Master alloys add the right amount of silicon, magnesium, zinc, or copper.
Return scrap is recycled castings that have no oil, paint, or dirt. - Use the right furnace.
A dry-hearth or shaft furnace keeps the dry oxide “skins” on top, instead of letting them sink into the melt. - Remove dissolved gas.
A spinning shaft bubbles argon (for aluminum and magnesium) or nitrogen with 0.5 % chlorine (for zinc) through the melt.
This strips out hydrogen and floats dross (the waste oxides) to the surface.
Quality target: Liquid aluminum for structural parts should hold no more than 0.15 milliliters of hydrogen in 100 grams of metal.
Move the Metal Gently
A thin oxide film forms on every molten surface. It is harmless until that skin is folded inside the melt—then it becomes a tiny double-sided crack and seeds porosity.
- Keep the flow smooth.
Metal should enter the gate at about 0.5 metres per second (a slow walking speed).
Below is the safe speed for three common alloys:
Alloy | Density (kg / m³) | Surface tension (N / m) | Safe gate speed (m / s) |
---|---|---|---|
Aluminum–silicon–magnesium | 2 380 | 0.90 | 0.50 |
Magnesium–aluminum–zinc | 1 750 | 0.55 | 0.42 |
Zinc alloy | 6 650 | 0.78 | 0.37 |
- Design the runner like a gentle funnel.
A tapered sprue, a small choke, and narrow runners keep the surface calm all the way into the die or sand mold.
Prepare the Die
- Pre-heat the tool-steel die to 180–250 °C.
This prevents the casting alloy from soldering (sticking) to the steel and reduces thermal shock. - Spray the cavities.
A water-based mix containing fine graphite or boron nitride coats the die.
The 80 % water flashes to steam, cooling hot spots and balancing die temperature.
4 Fill and Freeze the Metal
High-Pressure Die Casting (HPDC)
- Slow shot: Plunger pushes metal at 0.1–0.3 m/s along the sleeve.
- Fast shot: When the metal is close to the gate, speed jumps to 30–70 m/s and fills the cavity in under 0.06 seconds.
- Vacuum: Pumps pull the cavity down to 30–50 millibar so air can escape before the metal arrives.
- Intensification: Extra pressure feeds the metal while it solidifies, shrinking without pores.
Gravity and Low-Pressure Casting
- Gravity: Runners are sized so the flow stays calm; engineers aim for gentle, wave-free filling.
- Low pressure: A light pressure (about 0.7 bar above room pressure) pushes metal up a central stalk into the die. The flow is smooth and almost free of folded oxide—ideal for wheel rims.
Solidification begins in thin walls first; extra pressure feeds the thicker zones until the gate solidifies.
Eject and Trim the Casting
Ejector pins push the part out once it cools below 180 °C.
Extra metal from runners and overflows is removed in a trim press or by machining. Modern machines hold flash (the thin fin of extra metal) to below 0.1 mm.
Finish and Inspect
- Deburr and clean with shot-blast or vibratory bowls.
- Leak-test sealed housings by pressurising them with air under water.
- Heat treatment such as T6 improves gravity-cast aluminum, but is usually skipped for HPDC because any hidden oxide cracks can expand.
- Coatings:
- Aluminum → chromate-free conversion layer then powder-coat or anodise.
- Zinc or magnesium → e-coat plus paint.
Key Points to Remember
- Clean metal plus gentle flow equals strong castings.
- Gate speed around 0.5 m/s keeps oxide films on the surface where they belong.
- Vacuum and follow-up pressure are the twin tools for fighting porosity.