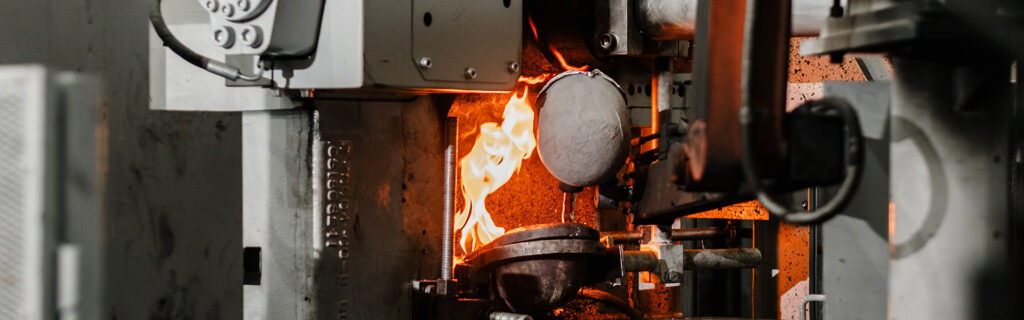
Advantages and Disadvantages of Die Casting
Use This Checklist Before You Commit Tooling Cash
Die casting delivers hundreds of millions of near-net-shape metal parts every year—from phone frames to EV drive-unit housings. But it is not a one-size-fits-all solution. This post weighs the hard benefits against the practical limitations so you can decide—early—whether high-pressure die casting (HPDC), gravity die casting, or sand casting will serve your technical and business goals.
Process Productivity
Metric | HPDC | Gravity Die Cast | Sand Cast |
---|---|---|---|
Cycle time (Al) | 20–60 s | 120–180 s | 15–30 min |
Typical batch size | ≥ 10 000 | 1 000–10 000 | 1–1 000 |
Well-controlled scrap | 2–5 % | 2–5 % | 5–15 % |
Advantage: A single four-cavity, 400-t HPDC cell cycling at 40 s spits out > 300 000 parts mo⁻¹.
Drawback: You only hit that cadence with robotic ladling, die-spray optimisation, and preventive maintenance—capex that low-volume programs cannot justify.
Dimensional Accuracy & Surface Finish
Linear tolerance (Al HPDC): ± 0.10 mm for the first 25 mm + 0.02 mm / 25 mm thereafter.
Surface roughness: Ra 1.6 µm (Al) to 0.8 µm (Zn).
Logos, serial numbers, and even light knurl textures survive e-coat or powder coat—saving engraving or secondary marking.
Trade-off: Ribs thinner than 1.5 mm freeze rapidly; if gate velocity, die temperature, or vacuum is off, you get misruns or cold shuts.
Mechanical Properties—Reality Check
Property (Al-Si alloy) | HPDC (vacuum) | Gravity Die Cast (T6) | 6082-T6 CNC billet |
---|---|---|---|
UTS (MPa) | 240 | 310 | 330 |
0.2 % YS (MPa) | 160 | 250 | 290 |
Elongation (%) | 4–6 | 8–10 | 12 |
Fatigue limit @ 10⁷ cy (MPa) | 55 | 70 | 90 |
Why the gap? Entrained bifilm oxides inside HPDC feed hydrogen-filled porosity. Vacuum fill, < 0.5 m s⁻¹ gate velocity, and in-cavity pressure can halve the gap, but gravity cast and wrought products still win where high-cycle fatigue rules (think suspension knuckles).
Tooling Economics & Break-Even
Tool | Cost (USD) | Typical life (shots) |
---|---|---|
Single-cavity HPDC (400 t) | 60 k – 90 k | 80 k–120 k |
Four-cavity HPDC (200 t) | 120 k – 160 k | 60 k–90 k |
Gravity permanent mold | 12 k – 20 k | 150 k pours |
Sand pattern + core boxes | 6 k – 12 k | replace yearly |
Break-even vs. sand casting typically falls at 6 000–8 000 units for a palm-sized part. HPDC’s higher capex is amortised quickly on automotive or appliance volumes, but hurts in niche or aftermarket runs.
Material Flexibility & Service Limits
Metal | HPDC suitability | Max service temp | Notes |
---|---|---|---|
Aluminum Al-Si | Excellent | 200 °C (as-cast) | Solution HT < 200 °C or blister risk |
Magnesium AZ | Good | 120 °C | Need SF₆-free cover gas |
Zinc Zn-Al | Best detail | 120 °C | Very low draft (< 0.25°) |
Copper, Brass | Gravity only | — | Too hot for H-13 dies |
Need UTS > 350 MPa, heat > 350 °C, or hermeticity?—look at squeeze casting, forging, or CNC billet.
Design Constraints You Can’t Ignore
Feature | HPDC Rule | Why it matters |
---|---|---|
Draft | ≥ 0.5° outside, 1° inside | Die life & ejection |
Wall uniformity | ± 20 % | Flow & solidification balance |
Blind pockets | Depth ≤ 3× wall unless vented/vacuumed | Gas entrapment |
Boss fillet | ≥ 0.4× wall | Hot spot → shrink |
These constraints often conflict with industrial-design goals—loop casting engineers in before A-surface freezes.
Quality Control Overheads
X-ray or CT for structural parts; reject criteria < 0.3 % porosity by volume.
Helium leak down to 1 × 10⁻⁵ mbar L s⁻¹ for e-motor housings.
Die thermal mapping every 5 000 shots—copper pin sensors or thermal cameras.
These steps add $0.10–$0.70 per part—but field failures cost far more.
Sustainability & Recycling
Die casting lives inside an 80 % recycled-aluminum loop; dross and machining chips are remelted.
Metric | HPDC Al | Injection-molded ABS |
---|---|---|
CO₂-eq cradle-to-gate (kg kg⁻¹) | 8.5 | 2.4 |
In-service CO₂ saved (light-weighting 1 kg in auto) | –25 kg lifetime | N/A |
While primary Al is carbon-intense, lightweighting still pays back within months of vehicle use.
When Die Casting Is Not the Answer
Annual demand < 5 000 parts—tooling never amortises.
Shot weight > 15 kg—few presses can fill reliably.
Post-heat-treatment above 350 °C—blistering & dimensional drift.
True hermeticity for high vacuum electronics—look at wrought housings or HIP after casting.
Summary Table
Attribute | Advantage | Disadvantage |
---|---|---|
Productivity | Seconds per shot | Needs automation & uptime discipline |
Accuracy | ± 0.10 mm achievable | Thin ribs risk misruns |
Strength | Up to 310 MPa UTS with heat-treat | Bifilm defects reduce fatigue |
Tooling | Low part cost at volume | $60 k+ upfront |
Sustainability | High recyclability | Higher CO₂ vs. plastics |
Design freedom | Cast-in threads, logos | Draft & wall uniformity strict |
Decision Flowchart
graph TD A[Part volume > 8000/yr?] -->|No| B[Choose sand or CNC] B --> End A -->|Yes| C[Wall ≤ 5 mm & weight < 15 kg?] C -->|No| D[Consider gravity permanent mold] D --> End C -->|Yes| E[Structural fatigue > 10⁷ cycles?] E -->|Yes| F[Gravity + T6 or squeeze casting] F --> End E -->|No| G[Select HPDC with vacuum & 0.5 m s⁻¹ gate] G --> End
Key Takeaways
HPDC rules high-volume metal parts under 15 kg that demand ± 0.1 mm accuracy.
Use vacuum + ≤ 0.5 m s⁻¹ gate velocity to close much of the property gap to gravity castings.
Break-even vs. sand casting sits around 6 000–8 000 pcs for hand-sized parts—check your BOM before cutting steel.
Where fatigue, temperature, or low volume dominate, gravity die, squeeze, or CNC billet may be better.
graph TD A[Part volume > 8000/yr?] -->|No| B[Choose sand or CNC] B --> End A -->|Yes| C[Wall ≤ 5 mm & weight < 15 kg?] C -->|No| D[Consider gravity permanent mold] D --> End C -->|Yes| E[Structural fatigue > 10⁷ cycles?] E -->|Yes| F[Gravity + T6 or squeeze casting] F --> End E -->|No| G[Select HPDC with vacuum & 0.5 m s⁻¹ gate] G --> End
Lexical error on line 4. Unrecognized text. ...dA -->|Yes| C[Wall ≤ 5 mm & weight < 15 ----------------------^